Resources
Automatic Replenishment
Introduction
Over the last decade manufacturers have been evolving from an MRP driven manufacturing model to a "demand pull" model for several good reasons.
Abandoning MRP … An MRP system is based on planned "builds". A computer model multiplies the planned build quantity times all of the components needed to make that product (bill of materials). These parts are then requisitioned, ordered, and staged in inventory in advance of the build. The build can't occur until the last part arrives and is received. Because of this, there is usually a flurry of expediting that occurs as the last parts trickle in and threaten to delay the build. The "scheduling" function is under severe pressure to coordinate the scheduling of various builds and all of the needed components, as consumer demand changes from one product to another, and as marketing revises forecasts at the last minute.
This process is virtually impossible to manage well. Inevitably, deadlines are missed, component inventory is too high for products that aren't being built, and there are lines down waiting for components that are needed. In addition, efficiency is compromised, as builds are broken down due to lack of components and less-needed products are built to keep the line running. And, most importantly it takes TIME to change the schedule. The manufacturing culture naturally resists changes in schedule because of the complexity of "re-planning" all the elements of the build. The end result is a manufacturing operation that is unable to react.
Changing to demand pull … The logic and culture of a demand pull system is radically different. Very modest inventories of all parts are maintained. Manufacturing is free to begin building as demand requires. When inventories reach a trigger level, a signal is sent for replenishment. This signal goes directly from the manufacturing floor to the vendor that is charged with replenishing the inventory. The inventory is then replenished on a very tight turnaround, in time for manufacturing to have complete flexibility to adjust build schedules.
This all takes place without involvement by planner-schedulers, expediters or manufacturing coordinators. It allows manufacturers to change lines quickly, and provides the support needed to make very small runs efficiently. And in turn allows the manufacturer to reduce finished goods inventory, because they can react more quickly to changes in demand for the final product. The result is lower inventories of both finished goods and components, lower management overhead, and all the cost benefits of a system that flows more smoothly.
Steven Label has tailored our systems to support the needs of demand-pull operations. We have systems in place to hold inventories, release them when signaled, and then rebuild according to a pre-determined plan. We have these programs in operation at several manufacturers. There are a variety of ways that this program operates in practice. It is the purpose of this document to describe the details and options for taking advantage of these very powerful concepts.
Program Description
The program is regulated by a master schedule of parts. An example of this schedule is shown in Exhibit A. The master schedule summarizes all of the parameters that govern the building, release and pricing of each part that is in the program.
Automatic Replenishment Program Summary
A | B | C | D | E | F | G | H | I |
Line | Part No. | Description | Build | Price | Ext = Max Liability |
Kan Ban Release |
Release Value |
Max Hold Period |
1 | 622679 | Label U.L. Outdoor | 104,000 | 0.0266 | $2,766.40 | 8,000 | $212.80 | 6 months |
2 | 626129 | Decoder Label | 20,000 | 0.2460 | $4,920.00 | 2,000 | $492.80 | 6 months |
3 | 627298 | Warning | 175,000 | 0.0350 | $6,125.00 | 25,000 | $875.00 | 6 months |
4 | 628697 | Raincheck | 16,000 | 0.1200 | $1,920.00 | 4,000 | $480.00 | 6 months |
TOTAL | $15,731.40 |
Startup. Steven Label will build and hold the quantity of parts shown in Column D - Build. If this part is being brought on line for the first time, we will ship 2 times the Kan Ban release quantity shown in Column G - Kan Ban Release. These are the start-up quantities that will be retained in the customer's assembly area, prior to use in assembly.
Signal. When the customer's assembly area exhausts the first bin quantity, a signal is sent to Steven Label, to release parts to replenish the used stock.
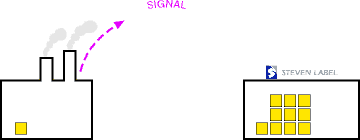
This signal can be done in any number of ways.
- A card can be pulled from the physical bin, and faxed to Steven Label.
- A phone call can be made.
- A bin can be scanned and the signal sent directly over the Internet.
- Steven Label personnel can periodically review the line-side inventory and send the signal directly, without the customer's involvement.
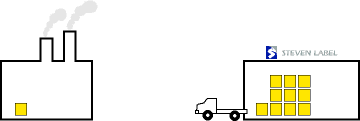
Release. Steven Label will ship the quantity shown in Column G - Kan Ban release, when the signal is received. The customer is invoiced for these parts at the time of the release, using the unit price shown in Column E - Price. This process continues until Steven Label ships the final release from the build, and has no inventory on hand.
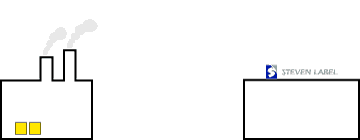
Rebuild. When Steven Label's inventory is exhausted, we will produce the quantity of parts shown in Column D - Build, just as we did at the beginning of the process. There are a number of options governing the procedures at this point. This is a logical time to check for pending rev changes or other changes that might affect the future of a part.
- Steven Label can rebuild parts automatically without customer involvement.
- Steven Label can notify the customer at the time, and proceed based on a verbal or written authorization.
- Steven Label can notify the customer so the customer can issue a purchase order to cover the next build. Internal control procedures often make it easiest to issue a new PO for each build. The packing list and invoice then references the new purchase order, so each build has it's own unique identity.
Maximum liability. In the event that a part becomes obsolete, before inventory is exhausted, the customer is responsible for the remaining inventory. If this happens just after a build occurs and before releases begin, the remaining inventory will be equal to the build quantity. Therefore the maximum possible liability is defined as the build quantity times the price. This is the value shown in Column F - Max Liability.
However, at any point in time, most of the parts will be in the middle of a build-release-rebuild cycle, so the actual liability will be well below the maximum. In any case, the customer is only responsible for the parts that have been built and remain unshipped.
End of program. The program can be terminated by no longer authorizing future builds. The remaining inventory can then be used to exhaustion, or shipped all at once.
Max hold period. The holding period is defined as the time a build authorization (purchase order) is received and the time the product ships complete, i.e. no remaining parts in inventory from that build. At the end of the max holding period, normally 6 months, the product must be shipped and billed. Under certain circumstances, we are willing to invoice the product and maintain the inventory at Steven Label.
Frequently asked questions
What determines the price?
Because this is a custom manufactured part, the price is based on the run quantity - in this case the build quantity. As in the assembly of any product that uses custom made parts, there is a balance that must be achieved between unit price, holding cost and the risk of obsolescence. In this program Steven Label bears the holding cost. The risk of obsolescence is borne by the buyer. Parts that have low risk of obsolescence can be purchased on a long horizon, large builds and the lowest possible unit price. Parts that have high risk of obsolescence should be purchased on a shorter horizon at a slightly higher unit price.
What is the optimum release size?
A mutually acceptable release size is chosen based on the size of the parts (inventory space required), their price per unit, and rate of usage. At a minimum, releases need to be sufficiently large, so there is time to build new inventory after the last release occurs. Given an average of 5-10 days to rebuild parts, a release should cover 2 or 3 weeks of usage.
As a matter of convenience, a release should have a value of at least $200. In addition, most label/overlay products take up very little space, so space requirements do not justify frequent releases.
How do line side services work in practice?
Steven Label personnel can take responsibility for reviewing inventory levels in an assembly area, and sending replenishment signals directly to Steven Label's plant. Normally this review takes place weekly. The customer gives the Steven Label person authorization to enter the plant (badge, pass, etc.). They enter the plant and go directly to the inventory location.
This has many fringe benefits. It is common for the Steven Label person to get to know the supervisor in the work area, so there is a natural and beneficial interaction that takes place. Steven Label receives direct feedback on any quality issues, and suggestions can flow to Steven Label about methods of packaging, identification, or any other variable. (This is no way compromises or minimizes the role of formal quality and performance feedback.) In practice, Steven Label becomes an extension of the customer's manufacturing operation, and the result is problems solved and improvements made with very little coordination needed.
In some cases, the Steven Label person will physically fill the inventory. In other cases, they send the signal to ship releases and the customer will refill the bins after performing a receiving function.
Who pays the freight?
Pricing is normally quoted FOB Steven Label. However, pricing can be based on FOB customer's location. In this case, the pricing would be based on a standard method of shipment. When rush shipments are required for reasons out of Steven Label's control, the customer is charged for the additional freight costs.